Types of sorbent circuits
Absorption circuit where the absorption and expulsion processes involve a coolant and a liquid absorbent. The pairs of working substances (coolant and absorbent) must be chosen so that they have different boiling points and be mixable without limitations with low mixing heat within the entire range of working temperatures and pressures.
Absorption circuit, using solid substances which adsorb the coolant to the surface under low temperature, and release it upon heat input under higher pressure. Such equipment operates periodically, which is a source of great losses and of a low cooling performance factor. At present, there is adsorption equipment with continuous operation (based on cold accumulation) working simultaneously with the heat pump and reaching higher energy efficiency compared to common industrial absorbent circuits. Its cooling performance factor is about 0.7 to 1.
This equipment which also works as a heat pump under continuous operation using a pair of working substances (zeolite – water) was developed by the Department of Production Technology of the Faculty of Mechanical Engineering of the Slovak University of Technology. It works as a functional prototype with a cooling capacity of 2.5kW and a thermal output of 15kW, and attains energy efficiency of approx. 1.3 of the coefficient of performance (cooling and heating factor).
Resorption circuit where the condensation and evaporation processes are replaced by resorption (recurrent absorption) and desorption (expulsion) processes. Such circuit is very complex, but offers highly cost-effective connection.
Diffusion circuit where the coolant evaporates in the evaporator and penetrates in the atmosphere of other gas by means of diffusion. This kind of circuit was used in home absorption refrigerators with ammonia as coolant, water as absorbent, and hydrogen as inert gas.
The use of heat in the absorbent chiller is beneficial from the point of view of the deployment of cogeneration units, as it allows the use of heat in summer out of the heating season, thanks to which the unit operation is extended. Heat consumption during summer is the major limiting factor given the size and efficiency of the cogeneration unit. The advantage of absorption chillers compared to compressor cooling units is the fact that they (almost) do not need any electricity, produce minimal noise, and are simple and reliable. The disadvantages include the need for high vacuum within the system, higher investment costs compared to traditional compressor cooling, larger size and weight.
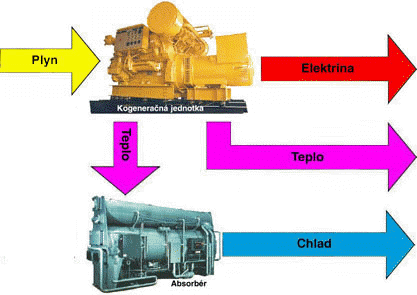
Industrially manufactured absorption cooling equipment use two pairs of working substances: NH3 – H2O (ammonia as coolant, and water as absorbent) for temperatures under 0°C, and H2O – LiBr (water as coolant, and lithium bromide as absorbent) for temperatures over 0°C.
Absorption cooling has three circuits among which heat exchange takes place. The first circuit is the hot water circuit (Qt) which is the driving agent for internal heat exchange. This circuit is connected to the heat source (a cogeneration unit, for example). The second circuit is a water circuit (Qs) directly connected to the cooling circuit (similar to central heating, but with cold water instead of hot water, cooling the air in rooms). The third circuit is a cooling water circuit (Qch) which takes away water with heat released by means of internal exchange for the purpose of cooling. The cooling is usually performed by means of cooling towers. The relationship between heats is as follows: Qch = Qt + Qs
The temperatures of the hot water circuit have a crucial impact on the size of the cooling equipment and, hence, on its price. In general, the higher the temperature of hot water, the smaller and cheaper the cooling equipment. Most industrially manufactured equipment works at a temperature range from 100°C to 135°C. The cold water circuit operates at temperatures needed for taking away heat from the given space. Such temperatures are generally between 7°C and 15°C. The cooling water circuit which takes away heat from the cooling equipment for cooling operates at a temperature range of about 20–45°C.
The coefficient of performance characterises the quality of the cooling process, i.e. the proportion between used cold and heat supply. A single-stage absorber (water – lithium bromide) is used to attain a coefficient of performance of around 0.65. There is absorption equipment cooling equipment using lithium bromide with a two-stage expeller, improving the coefficient of performance to 1.1. Such equipment is therefore suitable also for direct heating by means of natural gas, and can compete economically and in terms of energy consumption to equipment with electrically driven compressors.
In the absorption process of cooling with ammonia and water, the coefficient of performance depends on the evaporation temperature, e.g. 0.3 at -20°C and 0.5 at -5°C. In the ammonia – water system it is not possible to increase the coefficient of performance by means of multi-stage expellers. The ammonia absorbent has so far been used mostly in industrial applications in technological processes, especially when combined with the use of cheap waste oil. At present, there are various projects which aim to establish on the market also smaller units.
Those who have ever designed cogeneration know that it is a relatively complicated issue requiring a large number of input data. When designing an optimal solution for the combination of cogeneration and absorption cooling, the calculations must also be based on additional parameters that need to be taken into account. In general, the size of the absorption cooling unit is given by its cooling performance. The cooling performance both in heating and cooling is chosen with regard to the heat insulation properties of the object to be cooled. The required cooling capacity rate determines the heat performance of the cooling unit (heat output in warm water). In general, such output is approximately 1.3 times higher than that the cooling output. The size of the cogeneration unit is usually chosen on the basis of aspects other than the size of the cooling equipment; it is therefore necessary to examine whether the size of the heat output of the cogeneration is sufficient to operate the cooling equipment. If it is insufficient, it is necessary to obtain additional heat output, for example, in gas boilers. It is also possible to divide the output of the cooling units between absorption cooling and compressor cooling.
As previously mentioned, absorption cooling units are more demanding in terms of investment compared to compressor cooling units. The size and, hence, the price of the cooling equipment is determined by two basic parameters, namely: the cooling output rate and the temperatures of hot water. Since this data cannot be properly examined upon the first assessment, the indicative prices can have a relatively large range. It is therefore preferred to have a calculation for a concrete proposal for the cooling equipment size in accordance with concrete specifications. It is recommended to hold a joint meeting with the heating designer and with the supplier of the cogeneration unit in order to find a proper technical solution that would reduce the total investment costs of the cooling equipment.
An example of the application of trigeneration is its use in the administrative building of the Czech manufacturer of cogeneration units TEDOM in Třebíč where TEDOM cogeneration units are installed in combination with the YORK absorption chiller.